Revamping rotating machines
to meet today’s operational challenges
Current economic context requires process equipment to be more flexible than ever.
Pumps, compressors and steam turbines play a key role.
Rotating machines can be optimized to meet the industrial current challenges such as operating cost reduction, operational flexibility, higher efficiency and increased reliability. Here is how:
Pumps
Some technical adjustments are required when modifying operating conditions like increase or reduction of capacity and/or density product change. Depending on the pump technology and the new performance objectives, several options can be considered.
New objectives such as head, flow or new process conditions can be achieved when modifying internals such as resizing the impeller to keep the new operating point at the Best Efficiency Point and also significantly reduce electrical power consumption.
For multistage pumps operated at high speed and driven by a fixed motor, gear ratio change should be an alternative way to reach the new process flow without major modifications on the pump.
Additionally, the replacement of an existing electric motor can be considered when:
- The motor becomes oversized because of sustainable low flow operation (poor energy efficiency).
- The difference between design and new requested power as well as windings heating margin becomes too tight (overloading operation).
Generally speaking, every time there is a change in process parameters, a troubleshooting analysis should be performed to evaluate hydraulic (NPSH and low flow limits for operation, minimal valve sizing), electric (heating class for windings) and mechanical aspects (vibration limits at low flow and at high speed).
Centrifugal compressor
Centrifugal compressors are designed for given process parameters (pressure, temperature, molecular weight, mass flow) at a nominal speed with specific impeller and diaphragms design.
Here also, in case of significant change of the process parameters, a design review has to be performed to prevent major damages to the compressor or the driver while running them out of their operation windows. This could typically happen when running at low flow (surge) or at higher flow (overloading).
This design review may be performed by a third party without the Original Equipment Manufacturer.
Should the new process conditions bring the machine outside of its operation window, major upgrading may be considered, but in many cases no changes on the casing are required.
A significant efficiency margin can be achieved while installing a new cartridge (impellers and diaphragms with new design technology). For example, 15% more mass flow without impact on electrical power consumption has been achieved on a FCC wet gas compressor (see pics. 1 and 2).
Another option is the review of auxiliaries for a complete upgrading in terms of sealing (new dry gas seals mounting) or anti-surge protection (anti-surge valve selection).
In any case, pre-assembly in workshop is highly recommended to minimize the duration of the intervention on site during turnaround time.
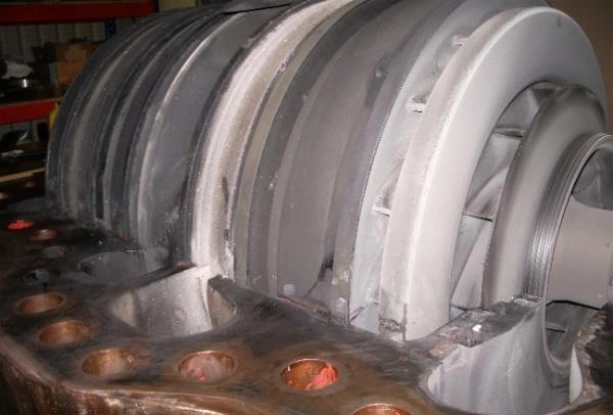
Picture 1 – Casing before revamping
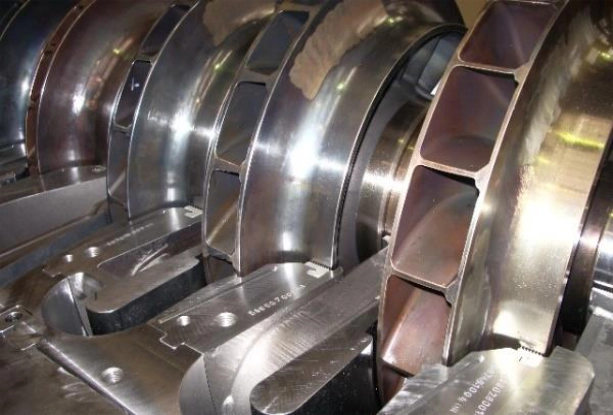
Picture 2 - Same casing with new internals and rotor, after revamping
Reciprocating compressor
Adaptation to new process conditions is easier to implement and less expensive for a reciprocating compressor since it is possible to adjust either the stroke or the piston’s diameter or the rotating speed.
Some examples on how to achieve either lower or higher flow are as
follows:
- In most cases for which the compressor frame is oversized, flow change can be achieved by adjusting the rotating speed without any major changes on the compressor.
- A new gear ratio can be sufficient to meet the new performance requirements for gear driven compressor equipped with motor having enough power margin.
- For direct drive compressor, the use of a new electric motor with a different number of poles will deliver the new required speed and power.
- Another way to increase or reduce the flow is to replace either the piston and the liner (new diameter) or the crankshaft (new stroke).
In all cases, particular attention needs to be paid to the bottles and diaphragms of the anti-pulsations protection therefore the system must be carefully checked. At the same time valves design, lube oil circuits and flow control devices need to be recalculated.
If the compressor is equipped with old step by step control flow devices, new technology of electro hydraulic control flow devices will be installed in order to reduce the electric power consumption (pic.3).
Steam turbine
A design review of internals (blades and diaphragms) should be made if power output is changed or if steam conditions differ from original design (pressure, temperature, backpressure or vacuum).
This review is mandatory if speed window operation differs from the original one. This will prevent blades failure (overloading) or rotor damages (overspeed).
New inlet valves design or change in the steam path definition (blades and diaphragms) are the best options to improve performances and reliability of the turbine.
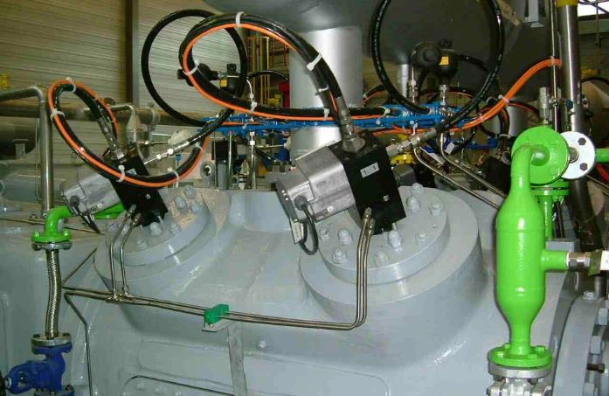
Picture 3 – New electro-hydraulic flow control device
Reducing power output can be achieved by decreasing steam inlet nozzle area.
Special repair methods have to be applied if existing rotor has been damaged in order to restore full performances of the turbine (disk repairs welding for new blades attachment).
Last but not least, second hand spare parts (internals and rotor) are a resourceful option to restart operations within few weeks after a major incident.
Air Blower
Air blower modifications may be done by a third party after new performances evaluation. There are several options to increase the capacity either by changing the impeller or adapting driver speed.
A detailed study has to be conducted to determine the best strategy. Sometimes a simple change of one or more impellers with higher efficiency is possible even without changing the existing casing. A special check of the driver is required for the turbine (maximal power and torque) or electric motor capacity.
Each case needs to be analyzed with regards of original data sheet and performance curves in order to determine if it is worthwhile to modify the blower or the driver.